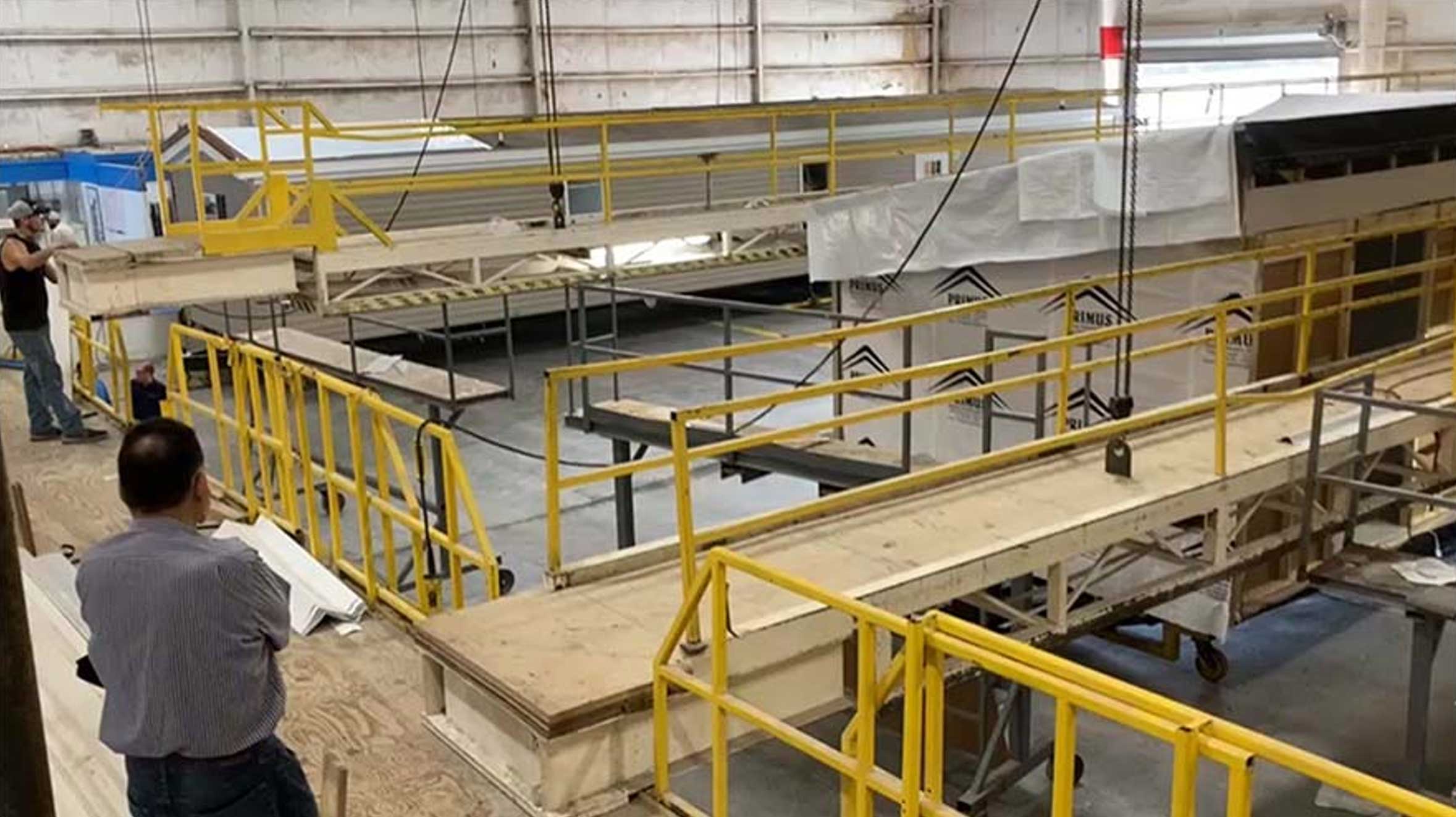
Large Mobile and Modular Home Manufacturer – Manufacturing Optimization – Value Stream Mapping
Our client approached us due to a need to increase their productivity and output of their modular and mobile pre‐manufactured homes. We provided this client with a current, future, and ideal value steam map of their facilities activities. The Value Stream Maps showed the flow of material from dock to dock which allowed for the analysis of all the steps involved. Design Systems, Inc. was able to implement many improvements without any capital expenditures required from the client.